Introduction:
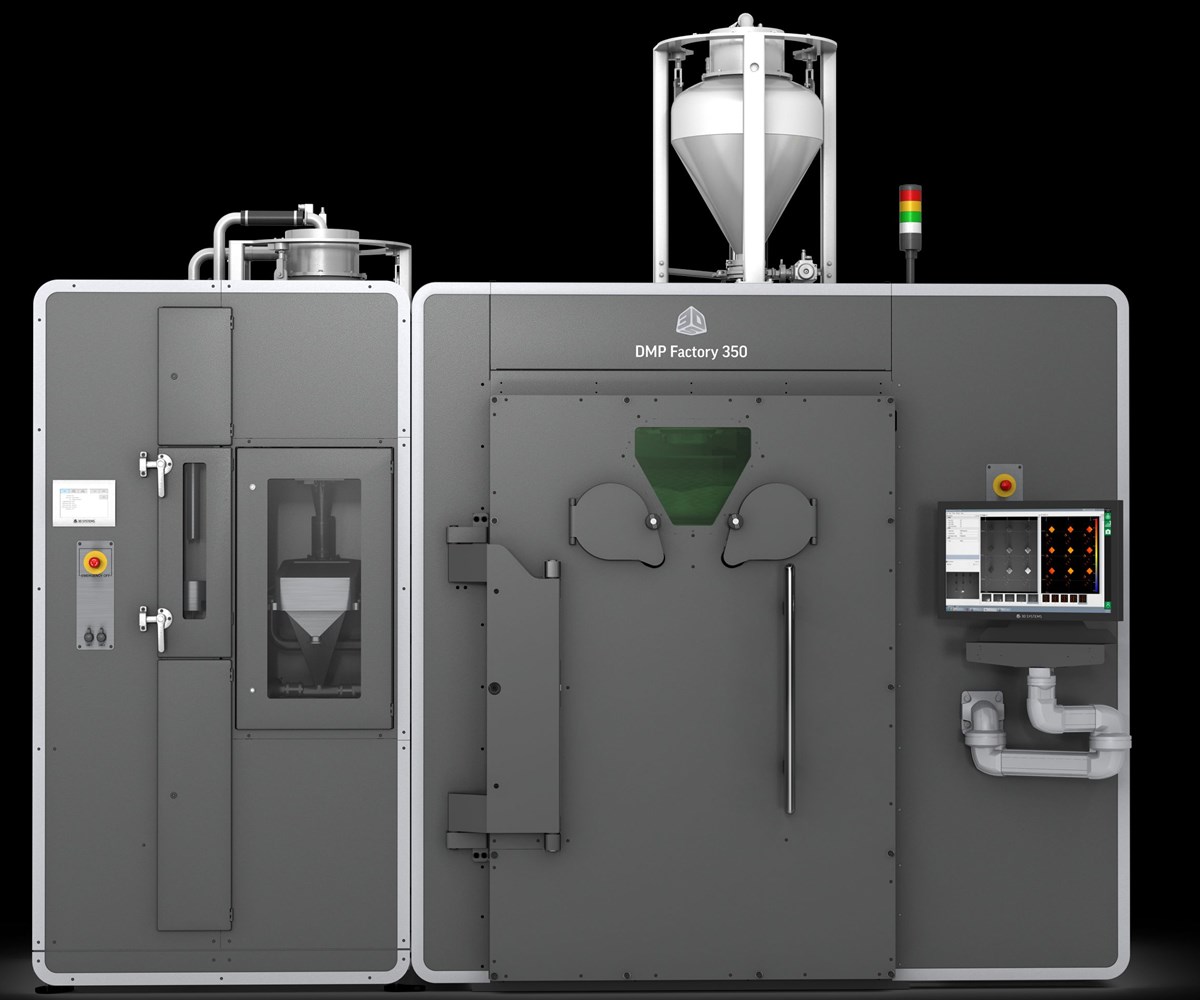
In today's fast-paced manufacturing industry, optimizing productivity and reducing machining costs are key priorities for any business. And when it comes to precision cutting, EDM (Electrical Discharge Machining) machines undoubtedly play a crucial role. In this blog, we will delve into the world of EDM cutting machines, exploring their features, benefits, and how they contribute to maximizing productivity and efficiency in various industrial sectors.
Understanding EDM Cutting Machines:
EDM cutting machines are specialized tools utilized for precision cutting and shaping of conductive materials. They employ the principle of electrical discharge to create complex and intricate designs with utmost accuracy. These machines offer superior performance over traditional cutting methods, as they are capable of cutting through materials that are considered difficult or impossible to machine using conventional techniques.
Benefits of EDM Cutting Machines:
1. Unparalleled Precision: Accuracy is of paramount importance in manufacturing processes. EDM machines provide micron-level precision, enabling intricate cuts and shapes that are impossible to achieve with other cutting methodologies. This accuracy translates into highly refined end products meeting the strictest quality standards.
2. Versatility: EDM machines can work with a wide range of materials, from metals and alloys to composites and ceramics. The ability to handle various materials grants manufacturers the flexibility to cater to diverse industry needs, leading to better market competitiveness.
3. Enhanced Surface Finish: The cutting method employed by EDM machines results in impeccable surface finishes, crucial for industries such as aerospace, medical, and automotive, where high-quality components are mandatory. Superior surface finishes reduce the need for time-consuming post-processing operations, further streamlining production.
4. Reduced Material Waste: Traditional cutting methods often lead to significant material wastage due to tool wear and the need for manual reworking. Conversely, EDM machines virtually eliminate the risk of tool wear, significantly reducing material wastage and associated costs.
5. Time and Cost Efficiency: As mentioned earlier, the time spent cutting is equivalent to financial gain. EDM machines optimize productivity by minimizing downtime and offering outstanding machine availability. This not only saves time but also significantly reduces operating costs, making them a cost-efficient option.
6. SMART and Connected Solutions: Leading manufacturers, including GF MS, offer SMART and connected solutions with their EDM cutting machines. Remote monitoring and real-time data analysis enable proactive maintenance, minimizing unplanned downtime, and further augmenting productivity.
Conclusion:
EDM cutting machines have revolutionized the manufacturing industry with their ability to deliver unmatched levels of precision, versatility, and cost-effectiveness. As manufacturing technologies continually evolve, it is imperative for businesses to invest in such cutting-edge equipment to remain competitive and meet the ever-increasing quality demands of customers. By optimizing productivity, reducing material wastage, and offering SMART solutions, EDM cutting machines hold the key to success in today's dynamic marketplace.
Keywords: EDM cutting machine, precision cutting, productivity, efficiency, electrical discharge machining, versatile cutting, surface finish, material wastage, time and cost efficiency, SMART solutions.